The History Of Firestop
Unfortunately, disasters caused the development of the firestopping industry.
The need for firestop systems became evident after an untested, unlisted material caused a disaster.
The following are examples of these types of disasters.
Browns Ferry Nuclear Plant - Alabama
Urethane Foam was used as a firestop material in electrical conduit penetrations through fire rated walls and floors. A fire started when a worker, trying to test the material for smoke containment, held a candle under the fire/air seal. When the seal ignited, and burned, the fire spread rapidly affecting critical control systems.
Other major fires around the country where the tragic loss of life and property could have been reduced significantly by the installation of proper firestop systems include:

MGM Grand Hotel
Las Vegas - 1980
85 deaths. - Sixty-eight people died from smoke inhalation on the 23rd floor of the hotel, even though the fire started on the first floor. Joints, shafts and egress stairwells allowed smoke to pass quickly to upper floors.
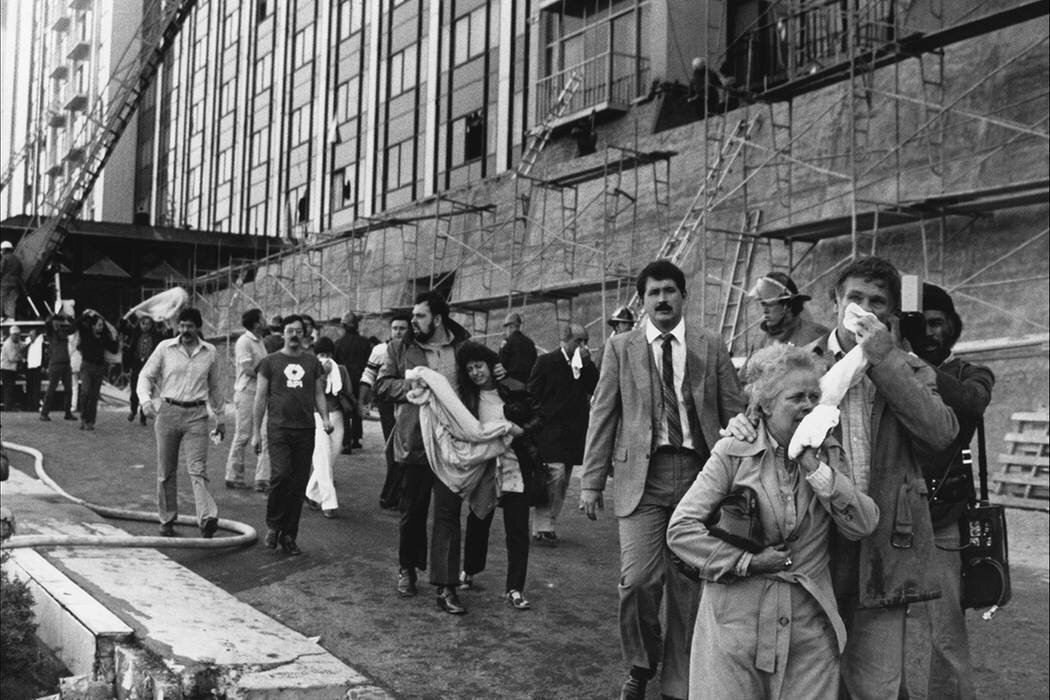
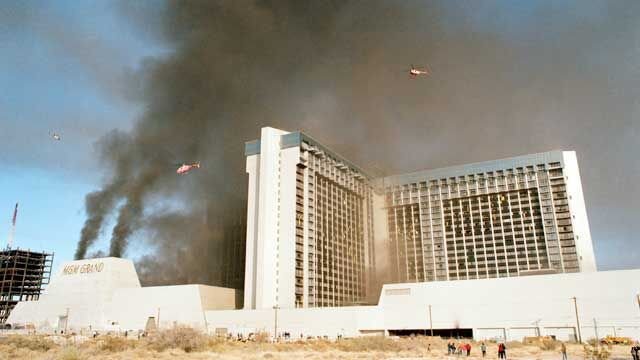
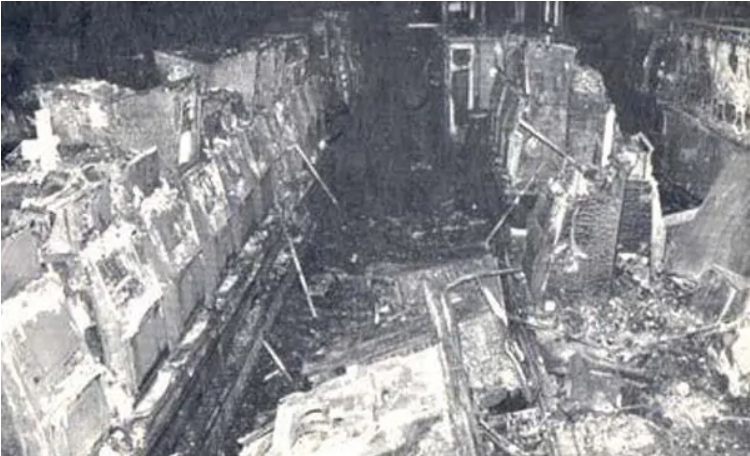

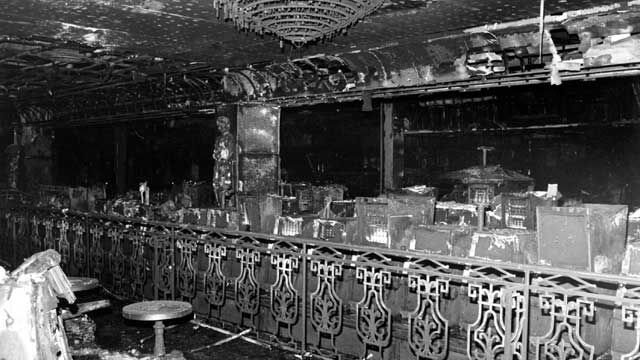
First Interstate Bank
-Los Angeles - 1988
$50,000,000 loss and 30 injuries in a late evening fire.
The sprinkler system was inoperable due to maintenance.
Meridian Plaza - Philadelphia - 1991
Multibillion dollar lawsuit, 3 deaths. The sprinkler system did not operate properly due to electrical failure at the controls.
Because of disasters like these,
National Code Organizations added provisions to their codes that require tested and listed firestop systems
(ASTM E-814/UL1479)
be installed in penetrations of walls, floors, gaps and joints.
These firestop systems prevent the rapid spread of fire, smoke and gasses between compartments reducing property damage and saving lives.
Through-Penetrations:
The Codes first required firestop systems for through-penetrations in the late 80's. There are currently over +10,000 tested and listed systems just for through penetration firestop. A contractor must be aware of the significance of the alpha- alpha - numeric code that tells the specifier, installer and inspector the construction type, the kind of penetrating item and identifies the manufacturer that obtained the listing.
Remember there is no one "miracle" product to do all types of through-penetrations. Most of the time it is a combination of materials that make-up the firestop system. It is also important to remember that no two manufacturers' installation instructions are the same.
The complexity of choosing the correct system requires up-front training and continuing education. Until quite recently, manufacturers of firestop products have taken it upon themselves to train those involved in an industry where various crafts do firestopping installation. Despite their efforts to provide the necessary training, misapplication of firestopping installations still occur with some frequency.
Non-Compliant Firestop
Proper Firestop Systems
Construction Joints:
Construction joint firestopping was not required until 1997. These applications include expansion joints, top or head of wall and curtain-wall or perimeter gap fire containment systems.
Expansion joints, due to seismic considerations, can be placed in numerous locations in floors and walls.
Top or head of wall applications include CMU, concrete and gypsum wall designs.
Curtain-wall or perimeter gap fire containment systems protect the opening where a rated floor assembly and an exterior wall structure meet. This wall assembly may or may not be a fire resistance rated exterior wall structure abutting the fire resistance rated floor assembly. There have been major losses due to lack of, or improper firestop systems at the perimeter gap.
Examples include:
Market Street Building, Philadelphia, PA (total loss)
First Interstate Bank and Occidental Towers, Los Angeles, CA,
The Hilton, Las Vegas, NV.
Many articles have been written about these disasters
These joint systems have one thing in common: Fire resistance and movement criteria of these independent substrates must be maintained.
This eliminates the accepted practice of using spray-on fireproofing, joint compounds and/or firestop mortar products for these types of applications
Shaft Alternative
The past several years have seen the development of flexible duct wrap materials for use as a fire-resistance-rated enclosure for kitchen grease ducts and HVAC ducts and as a method of reducing clearance to combustible materials.
These flexible wrap materials typically consist of a highly insulating lightweight flexible blanket made of, inorganic, fibrous refractory material. The duct wrap blanket may be un-faced, faced on one side or fully encapsulated in an aluminum foil, reinforced with scrim. The difference between the fully encapsulated blankets and the others are both the faces and edges of the blanket are sealed so that no portion of the blanket core is exposed. This encapsulation is intended to protect the blanket core from wicking moisture, grease or condensation, thus minimizing potential fire hazards and increasing the life of the blanket.
Remember these applications are governed by a tested and listed system also.
Building Codes:
Federal, state and local government agencies have adopted rules which specify minimum requirements to building construction. Some states have adopted a uniform statewide building code, while others delegate code adoption to counties and other entities within the state.
In the absence of a uniform set of firestop standards, architects and engineers must design firestop systems according to multiple codes and will probably be held to compliance with the most stringent. As a result, many architects, engineers, inspectors and code officials are confused about which standards to follow when designing and inspecting firestop systems.
Liability:
All entities involved in a construction project or building fire may be held liable for a firestop system, or lack thereof. Owners, architects, engineers, consultants, contractors and suppliers can all be held responsible for damages arising from the installation, design, or lack of a firestop system.
Firestop systems must be assembled as tested (100% without exception) before a rated system can exist. After selecting the proper test for a through penetration firestop, that test must be followed.
The floor or wall must be assembled as tested and rated, caulk, wrap strip or other firestop materials must be installed as tested. Any variance in the manufacturers installation instructions nullifies the system making the assembly only a hole in a fire-rated floor or wall, filled with something that may not perform in a fire.
In the firestopping business, if an installer, estimator or other person misses a parameter, whether intentional or not, it could potentially cause loss of life, property damage or interruption in continuity of operations.
Therefore, it's important to install to the tested and listed system specifications. Firestop installing must be viewed as a "zero tolerance" item.
If the specifications of a tested system are not followed, the system may not work, rendering the investment in building protection useless.